

Shelf Model Storage System is based on the standard of having safe and sound solutions for tool storage. That would be 4500 lbs draw bar force multiplied by 4 (ish) 18,000 lb draw bar force, approaching the maximum clamping force (for example for a C-6 interface - by comparison ).Description CNC Tool Cart Capto C6, Shelf Model, 105 Holders capacity 20KN (Killo Newton) draw bar force being multiplied to a 80 KN clamping force at the connection. The KM 4X being a roughly 4X multiplier of the initial draw bar force. Seems Capto would be the most secure also ? BUT not sure how that would theoretically or practically compare to the NEW -Newer- Newish KM X4. i-200 or i-300 or Mazak's much larger machines (like a INTEGREX e-670H) or for that matter the draw bar forces on the Okuma Multus machines or DMG Mori Mill turn machines of different sizes.įor Integrex (mill turn) there are instances when there is no lower turret and therefore the bending moment of turning tools is more critical - thinking longer flash tooling type - 3 turning tools on one tool holder (indexable) at the B axis milling spindle (axis). I'm not sure exactly what the draw bar forces are exactly for different integrexes i.e. other than the rotational repeatability that -MariTool- mentioned. (smaller machines and smaller in cut loads seems HSK would suffice. Maybe what is getting at is the NEW KM4X interface ~ which apparently (HSK) machines can be retrofitted for ?īasic draw bar force for comparison of the different connections can make a real difference. KM is also an option offered even for new machines as an option.
#CAPTO C6 HOLDER UPGRADE#
Not really the case any more.įor new / newer MAZAK integrex(es) for some reason they offer HSK as standard and Capto (in the case of a C-6 machine ) is about a $4000 upgrade factory ordered for a new build. Years gone by it was almost mandatory to have a lower turret on a b axis machine to be able to hold tolerances on turned features (so I'm told). I think it's becoming more common to specify machines in this configuration generally, as the technology improves. Doing everything on the b axis head keeps everything simple and flexible at the cost of production efficiency. We specified our NTX without a lower turret because the most important criteria to us was quick changeovers for one-two off parts. HSK also can't be used for building modular tool assemblies, whereas Capto excels at that too. HSK may be easier to balance for very high speeds compared to Capto, but I think that is even marginal tbh. HSK rules in milling spindles because it provides all the benefits of Capto that matter in that scenario, while being a much cheaper spindle to make, and cheaper tools to buy. I think what it boils down to is that HSK doesn't have any direct benefits over Capto beyond cost.
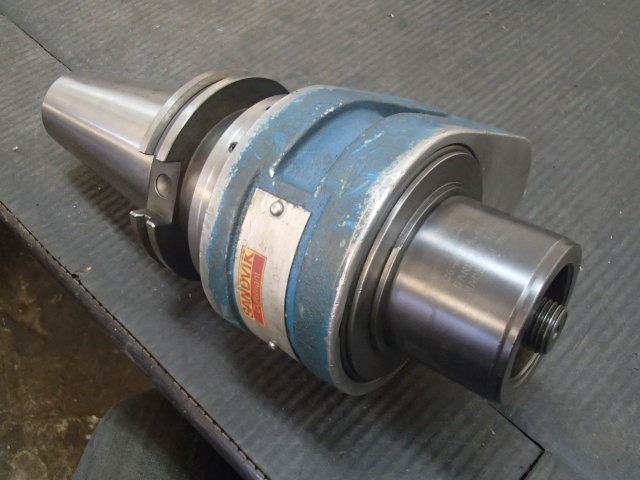
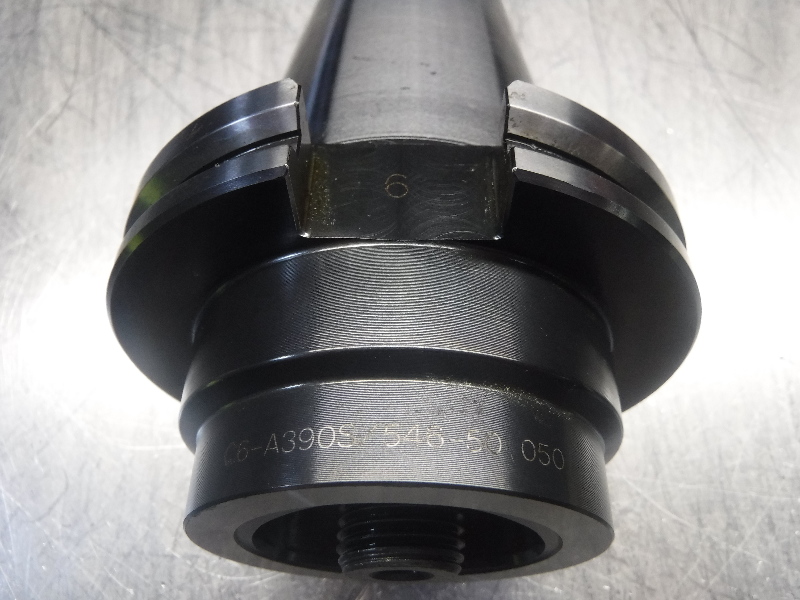
Those are solid arguments and all totally correct.
#CAPTO C6 HOLDER ISO#
The options for milling holders are probably greater on HSK, but I've never struggled to get what I need on Capto.Ĭapto holders are generally a bit more expensive than HSK holders, all else being equal, so you need to consider that.Ĭapto is pretty much the de-facto standard on all new millturns these days anyway, and is now an ISO standard (ISO 26623, generally called PSC) rather than being a proprietary Sandvik product, which means that there are many manufacturers of Capto/PSC tools now.Īvoid KM at all costs, it is an orphaned system that never saw wide scale adoption by anybody except Mazak on early integrexes, and while Kenna still make it, you have to wonder whether they will continue to do so for very long. The options for turning tools are much greater on Capto than on HSK-T. HSK-T is a bit of a kludge that was developed to try and match Capto for torsional rigidity and repeatability, but it falls short on both. It's just as good as HSK for milling, and much better for turning.
